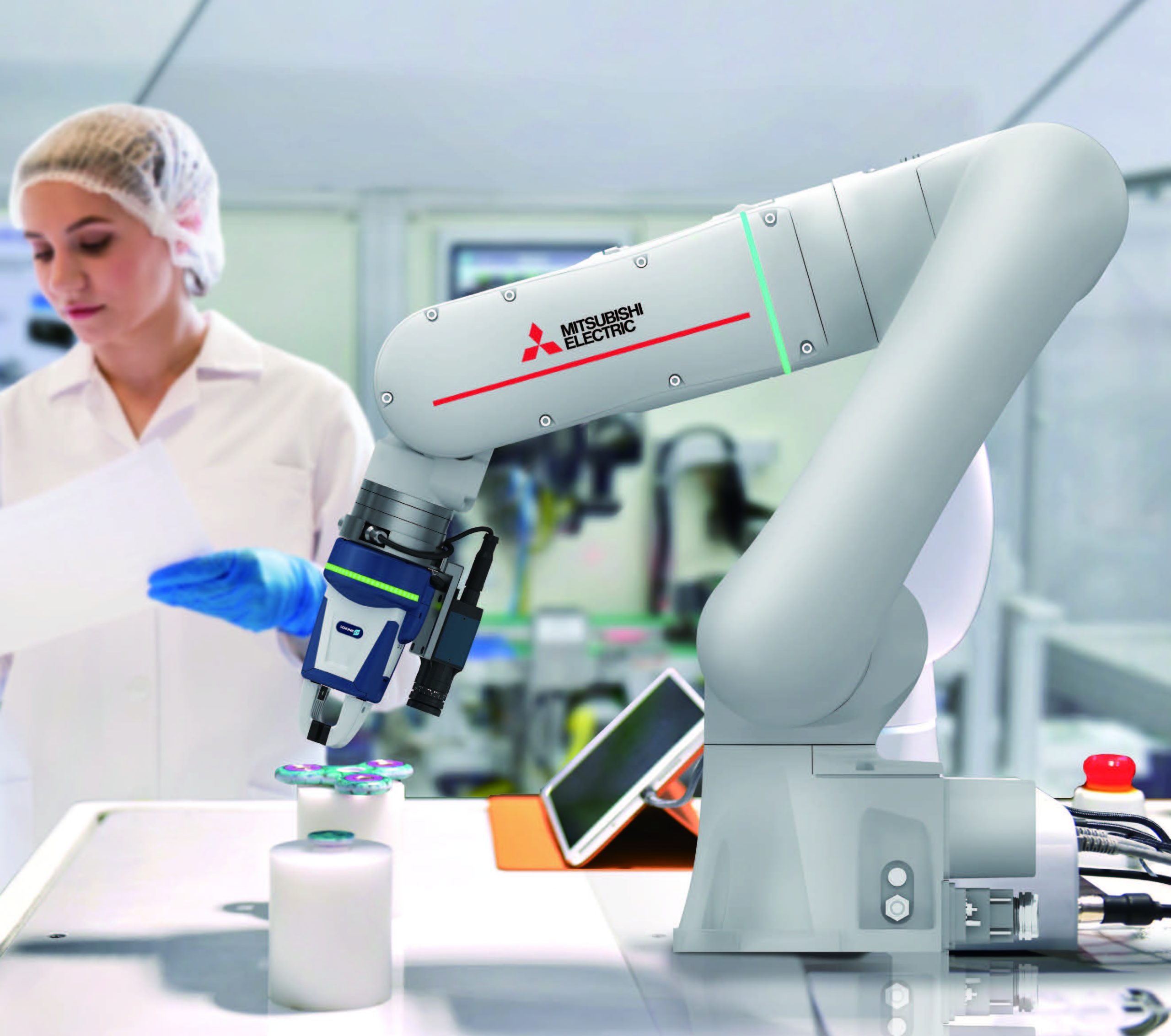
Collaborative robots provide immense value in a manufacturing setting. These robots work side-by-side with humans to increase safety, output, and quality. Sometimes referred to as “cobots,” they’re a valuable tool in a plant’s manufacturing line.
It helps to understand what cooperative robotics covers. While you might think of a robot working fully on its own, a collaborative robot requires human help. It cannot work without human involvement.
Think of it like the robotic surgical arm that’s controlled by a surgeon at a control panel, but the robot makes the tiny incisions. The same human-robot collaboration carries over into many fields, including manufacturing. They help out in many ways, but these four applications top the list.
Four Ways to Use Collaborative Robots in a Manufacturing Setting
Take a closer look at the most common uses for cobots in manufacturing processes.
Assembly
Not every plant requires assembly, but when it is a component of your manufacturing process, it must be done correctly. Face it, rote tasks tire people out. When you’re doing the exact same thing over and over and over, you’re going to start making mistakes hours into it.
A recent automotive recall occurred when a component within the steering system wasn’t assembled correctly. This mistake can cause the steering system to become sluggish, making it harder to steer. Over 43,700 vehicles are affected and must be returned to the dealer for repair. With cobots helping out, the risk of error is lower, and your worker and a collaborative robot team up to ensure quality control measures are followed.
Machine Tending
Machine tending is defined as the process of loading or unloading a machine. Your workers can have a robotic arm or arms to load heavy items into a machine’s hopper or place something like a heavy spool onto the arm of an extruder machine. When the manufactured item is done, a collaborative robot can lift it off, which eliminates the risk of a muscle tear or strain from having to lift something heavier than a worker can handle.
For example, you own a plant where workers coat bare wire with an insulative, waterproof coating. Workers must climb a ladder with a 50-pound box of plastic pellets, empty them into a feeder, climb back down, and place a spool of bare wire into the machine. A second empty spool for packaging It’s an intense job that requires upper-body strength and product loss is costly.
With the help of collaborative robots, the strain on your workers’ backs, legs, and arms is lowered. There’s less risk of muscle strain and workplace injuries, and there’s also less room for mistakes or damage caused by dropped pellets or spools.
When there are changeovers from one color of plastic pellet to another, cobots do it faster. It’s not going to make a mistake that a human might make, such as needing the color marked 021 in the barrels and accidentally getting 012 instead.
Material Handling
Another valid use of collaborative robots is the repetitive tasks that happen throughout the manufacturing process. You can have them assist with picking, packing, and palletizing. While a worker puts the finishing touch on a product, a cobot could be folding and gluing a box for the item to go into or vice versa. Ideally, the robot does the heavy lifting or working at an unusual angle, which lessens the strain on your employees’ bodies. It reduces the risk of workplace injuries.
Another benefit is that the robotic arms have grippers that prevent damage from a dropped product. Humans are prone to errors, and even when it’s accidental, it can be costly. Cobots help prevent accidental damage and loss.
Once items are constructed and checked for quality, cobots can help package them correctly, package those items into boxes or shipping containers, and prepare them for pallets. You can add additional automated equipment to stack pallets, wrap them, and load them onto trailers.
Quality Control
Finally, collaborative robots are ideal for quality control. They can use laser and AI technology to visually inspect products to ensure the quality is consistent during each step of the production process. If something is off, you get the alert and adjustments can be made before products are completed and sent to the public.
It boosts quality control and eliminates scrap and wasted materials. This saves money and prevents harm to your company’s reputation. Just one recall due to defects or poor quality can be costly.
A massive airbag recall occurred when it was found the propellant wafers weren’t properly used with a chemical drying agent. Humidity can cause the propellant to rupture, causing the airbag inflator to rupture and send metal shards into the cabin. The older the car, the bigger the risk of this happening. Quality control is essential in any area of manufacturing.
Mitsubishi Electric’s ASSISTA Collaborative Robot
Mitsubishi offers the ASSISTA collaborative robot, as well as many other robotic and automated tools to heighten safety, efficiency, and productivity in your manufacturing plant. ASSISTA is a collaborative robot that’s easy to use and has a teaching panel that helps operators and robots work together without difficulty. Among the many features are:
- Computer and programming experience are unnecessary.
- Hand-guided operation that pairs with a teaching panel on the device rather than on another controller.
- Industrial-grade gearboxes ensure durability, even with excessive use.
- Internal wiring eliminates damage or safety issues.
- An LED light ring shows when the robot is in collaborative mode.
- Next-gen servomotors heighten safety.
- The slim, lighter arm design provides ease of installation, comfort, and safety.
Industrial robots from Mitsubishi all use the same programming language, so you can pair collaborative robots with SCARA and vertically articulated robots. Software is backward compatible, so if you decide to add additional robots in the future, you don’t have to upgrade the software every time.
Talk to the experts at Mitsubishi to learn more about collaborative robots in your manufacturing plant. We work with our clients to ensure they have the best equipment for their production needs.
Work with Us and Succeed
We love our customers and the challenges they bring to us. We also like to let our customers shine by discussing how we worked together to solve their biggest challenges. If you have a challenge that needs to be solved and would like to be our next BIG success story, reach out to us and let’s connect!
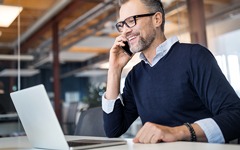